Let us collaborate to foster global growth and development together.
Integrated Manufacturing Systems
Explore Integrated Manufacturing Systems (IMS) and how they optimize production efficiency. Understand key benefits, challenges, and future trends shaping manufacturing today.
6/30/20074 min read
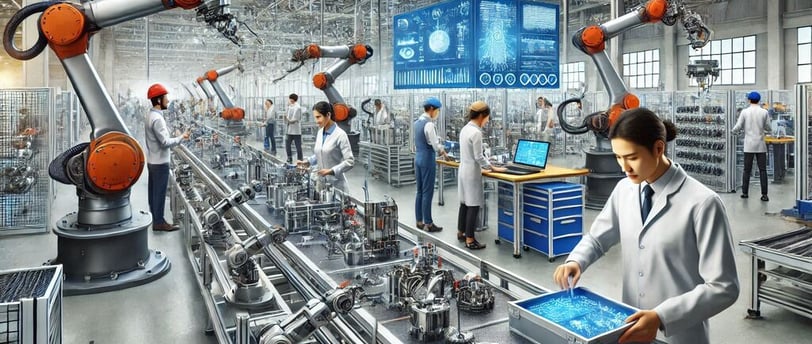
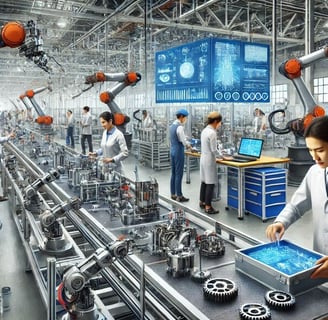
Meta Description:
Explore Integrated Manufacturing Systems (IMS) and how they optimize production efficiency. Understand key benefits, challenges, and future trends shaping manufacturing today.
Integrated Manufacturing Systems: Revolutionizing Production Processes
In today’s fast-paced manufacturing world, efficiency and flexibility are paramount. One approach gaining traction is the implementation of Integrated Manufacturing Systems (IMS). By seamlessly linking production processes, IMS allows businesses to streamline their operations, enhance product quality, and reduce costs. But what exactly are Integrated Manufacturing Systems, and how do they improve the manufacturing environment? Let's take a closer look.
What Are Integrated Manufacturing Systems?
An Integrated Manufacturing System (IMS) refers to the use of information technology to integrate various aspects of the manufacturing process. This includes linking different production stages, machines, employees, and data to work together seamlessly. IMS helps create a real-time, automated flow of information that improves decision-making, process control, and overall productivity.
Core components of IMS include:
Robotics and automation: These streamline repetitive tasks, reducing the need for manual labor and increasing accuracy.
Enterprise Resource Planning (ERP): This connects various aspects of the business, from inventory to finance, ensuring data flows smoothly between departments.
Manufacturing Execution Systems (MES): MES track and monitor the progress of products as they move through the manufacturing process, ensuring efficiency and reducing waste.
Key Benefits of Integrated Manufacturing Systems
1. Improved Efficiency and Productivity
One of the most significant advantages of IMS is its ability to improve production efficiency. By linking machinery, software, and people, IMS reduces downtime and ensures that processes are optimized for speed and accuracy. Automated data collection and real-time tracking of production stages help identify bottlenecks, streamline workflows, and ensure smooth operations across the factory floor.
For example, an automotive manufacturer using IMS can monitor real-time data from machines and workers, instantly identifying delays, malfunctions, or inefficiencies. With this knowledge, they can quickly adapt and make adjustments, minimizing costly downtime.
Top productivity gains from IMS:
Reduction of manual interventions
Reduction in setup time and production delays
Streamlined inventory and material management
2. Enhanced Quality Control
Ensuring high-quality products is a core concern for manufacturers, and IMS plays a crucial role in maintaining standards. With real-time monitoring and automatic adjustments, IMS can identify deviations from set standards during the manufacturing process. Whether it's material defects, incorrect machine settings, or process flaws, these systems can instantly alert operators to problems, enabling swift correction before defective products are created.
Quality control benefits of IMS:
Consistency: Ensures each product is manufactured to the same high standard.
Precision: Automated systems reduce human error and improve precision in production.
Real-time analytics: Operators can access data that helps pinpoint and correct errors instantly.
3. Cost Reduction and Resource Optimization
Reducing costs while maintaining product quality is a delicate balance in manufacturing. IMS provides businesses with powerful tools for minimizing waste, optimizing resource use, and maximizing profitability. By leveraging real-time data, IMS can better manage inventory, schedule production runs efficiently, and reduce overproduction or stock shortages.
For instance, a manufacturer using an IMS can predict the amount of raw material needed for each production cycle, which ensures they order exactly what’s necessary. This precise ordering reduces costs associated with excess inventory or out-of-stock situations.
Ways IMS cuts costs:
Minimizes waste and improves resource allocation
Reduces energy consumption by optimizing machinery usage
Streamlines supply chain management, reducing stockholding costs
Challenges and Considerations for Implementing IMS
Despite its advantages, implementing an Integrated Manufacturing System isn't without challenges. As manufacturing operations become more interconnected, businesses need to ensure that their IMS is properly integrated with existing software and hardware.
1. High Initial Investment
The cost of implementing an IMS can be a significant hurdle for smaller manufacturers. From the software systems (ERP, MES, etc.) to the robotic machines and automation technologies required, the initial investment can be substantial. However, many manufacturers find that these systems pay off in the long run by reducing labor costs and improving operational efficiency.
2. Change Management
Adopting an IMS often requires significant changes to the way employees work. This can be a challenge for businesses with long-standing manufacturing processes. Employees may require extensive training to understand and utilize the system effectively. Ensuring that workers are comfortable with new technologies and processes is crucial for a smooth transition.
3. Data Security
With the vast amount of data being processed in an IMS, companies must ensure that sensitive information is protected from cyber threats. Adequate cybersecurity measures, like encryption and secure network access protocols, must be in place to safeguard against potential breaches.
Future Trends in Integrated Manufacturing Systems
As technology continues to evolve, so too will Integrated Manufacturing Systems. Here are some trends to watch for in 2024 and beyond:
1. The Rise of Artificial Intelligence (AI) and Machine Learning
AI and machine learning are transforming the manufacturing landscape. These technologies allow IMS to not only analyze real-time data but also predict potential issues and opportunities based on patterns recognized in past production data. As AI evolves, it will become increasingly capable of self-optimizing manufacturing processes, driving even higher efficiency and lower costs.
2. Integration with the Internet of Things (IoT)
The Internet of Things (IoT) is expanding rapidly in the manufacturing sector. IMS systems are being integrated with IoT devices to improve communication between machines, equipment, and workers. Sensors placed on equipment allow manufacturers to gather valuable data to anticipate maintenance needs, detect anomalies, and ensure optimized operations in real-time.
3. Cloud Computing and Remote Monitoring
Cloud computing will enable manufacturers to access IMS from anywhere in the world, with remote monitoring allowing for increased flexibility and control over operations. This trend is especially valuable in industries with multiple production facilities, as it allows managers to oversee operations in real-time, from a central location.
Conclusion
Integrated Manufacturing Systems are changing the face of production by offering manufacturers improved efficiency, reduced costs, and better quality control. While implementing IMS requires a thoughtful approach and investment, the benefits make it clear that these systems are more than just a trend—they're the future of manufacturing. Businesses willing to embrace these technologies will gain a competitive edge in a rapidly evolving industry.
Engage with Us: How is your business adopting Integrated Manufacturing Systems? Share your experiences or thoughts in the comments below!
Innovation
Cutting-edge solutions for industrial efficiency and productivity.
© 2024. All rights reserved.
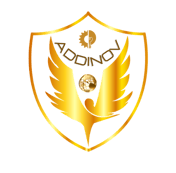
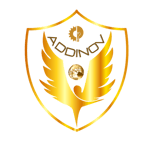