Let us collaborate to foster global growth and development together.
Compréhensive Factory Audits
Learn how comprehensive factory audits ensure product quality, regulatory compliance, and operational efficiency. Explore key benefits and best practices.
3/20/20073 min read
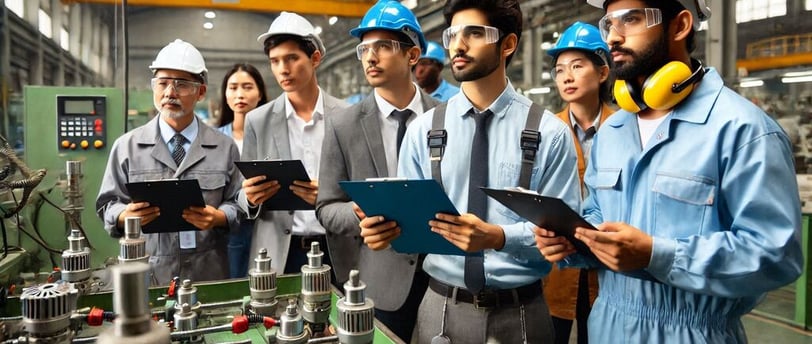
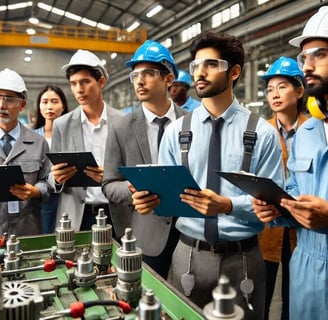
Comprehensive Factory Audits: Ensuring Quality and Compliance
Meta Description: Learn how comprehensive factory audits ensure product quality, regulatory compliance, and operational efficiency. Explore key benefits and best practices.
Introduction
Imagine partnering with a manufacturer only to discover flaws in production processes that compromise quality. Such oversights can damage your brand reputation and cost significant resources. Comprehensive factory audits are the solution to preventing these issues, offering a systematic way to assess and verify a facility’s compliance, capabilities, and standards.
Why Are Comprehensive Factory Audits Important?
Comprehensive factory audits are vital for businesses that value consistent quality and regulatory compliance. These assessments go beyond surface-level checks, offering deep insights into a factory’s operations.
Key Benefits of Factory Audits:
Quality Assurance: Verify that manufacturing processes meet predefined quality standards.
Risk Mitigation: Identify and address potential risks before they escalate into larger issues.
Regulatory Compliance: Ensure adherence to local and international manufacturing laws and standards.
Cost Efficiency: Detect inefficiencies to reduce waste and streamline operations.
For example, many global brands rely on factory audits to maintain their reputations while optimizing their supply chains.
Core Components of a Comprehensive Factory Audit
A well-structured factory audit involves various aspects to provide a holistic view of the manufacturing facility. Let’s delve into the critical elements.
Quality Control Processes
Inspect the facility’s quality control systems, ensuring they align with industry standards. This includes:
Reviewing production workflows
Evaluating testing methods
Checking documentation and certifications
For example, ensuring ISO 9001 certification confirms the factory adheres to international quality management standards.
Safety and Compliance Checks
Factory audits must evaluate:
Worker safety practices
Equipment maintenance
Compliance with local labor laws and international guidelines
Such practices ensure employee well-being and protect businesses from legal repercussions.
Capacity and Capability Assessment
Assess the factory’s production capacity to confirm it meets your order demands. This includes evaluating:
Equipment and technology
Staff skills and experience
Supply chain reliability
Ethical Standards Evaluation
Ethical audits ensure the factory operates responsibly. Areas assessed include:
Fair labor practices
Environmental sustainability
Ethical sourcing of materials
These factors are especially critical for brands with a focus on Corporate Social Responsibility (CSR).
Common Challenges in Factory Audits
Even with meticulous planning, conducting factory audits can pose challenges. Understanding these obstacles can help businesses prepare and overcome them effectively.
Resistance from Suppliers
Some suppliers may hesitate to undergo audits due to fear of exposure or disruptions. Clear communication about the benefits and collaboration opportunities can ease such concerns.
Logistical Complexity
For global supply chains, coordinating audits across various locations can be challenging. Leveraging third-party audit services can simplify the process.
High Costs
Comprehensive audits can be resource-intensive. However, the long-term savings from preventing production errors outweigh the upfront costs.
Best Practices for Effective Factory Audits
To maximize the benefits of factory audits, follow these best practices:
Develop Clear Objectives
Before initiating an audit, define your goals. Are you focusing on quality control, compliance, or overall operational efficiency? Clear objectives ensure targeted assessments.
Use Skilled Auditors
Engage experienced auditors familiar with industry standards and regional regulations. Third-party auditors offer unbiased assessments and industry expertise.
Foster Transparent Communication
Share the audit process and expectations with the factory management. Transparency builds trust and encourages cooperation.
Leverage Technology
Digital tools like audit management software enhance efficiency and data accuracy. These platforms streamline documentation and reporting, ensuring a thorough evaluation.
Case Study: Effective Factory Audits in Action
A leading apparel brand faced quality inconsistencies from a supplier. After conducting a comprehensive factory audit, they identified gaps in the quality control process and worker training. By implementing targeted improvements, the supplier’s defect rate dropped by 25%, significantly enhancing product quality and delivery timelines.
Future Trends in Factory Audits
As industries evolve, so do factory audit practices. Here are some emerging trends:
Digitalization: Technology like AI and IoT is automating audit processes, improving accuracy and efficiency.
Sustainability Focus: Increasing emphasis on environmental audits to meet eco-friendly standards.
Remote Auditing: With advancements in virtual tools, remote audits are becoming feasible, reducing travel costs and time.
Practical Steps to Initiate Your Factory Audit Program
Select the Right Audit Type: Decide whether you need a full-scale comprehensive audit, a quality-focused audit, or an ethical compliance audit.
Choose Reliable Auditors: Partner with reputable third-party auditors who bring expertise and objectivity.
Create an Actionable Checklist: Document all areas for assessment to ensure a systematic approach.
Analyze Findings and Take Action: Use audit results to implement necessary improvements and monitor progress.
Conclusion
Comprehensive factory audits are indispensable for businesses aiming to maintain high standards in quality, compliance, and operational efficiency. By investing in thorough assessments, companies can safeguard their reputation, meet customer expectations, and achieve long-term success.
Are you ready to take the first step in optimizing your manufacturing operations? Share your thoughts below or explore our related articles on quality assurance and supply chain management for more insights.
Internal Links Suggestion: Check out our article on “Supplier Selection Strategies” to complement your factory audits with smarter partnerships.
Innovation
Cutting-edge solutions for industrial efficiency and productivity.
© 2024. All rights reserved.
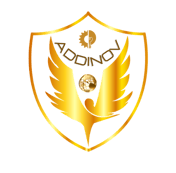
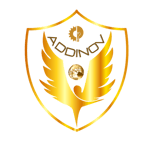